Which moisture mitigation strategy?
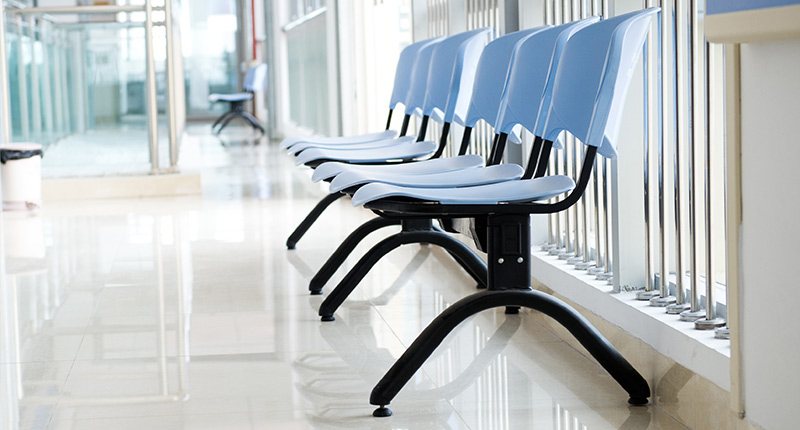
Excess moisture in concrete slabs is a common issue, whether working on new construction or a renovation. In new construction, accelerated project schedules may not allow time for the slab to fully dry—a process that can take several months. In renovation projects, older slabs may not have adequate waterproofing or the moisture barrier membrane may have become compromised over time. Whatever the reason, mitigating the problem before installing finished flooring is critical to avoid a costly failure. But what mitigation approach is right? The answer may depend on your specific project circumstances.
One approach is to use a reactive penetrant or a concrete additive to help accelerate the drying process and prevent moisture passage by closing the capillaries in the concrete. This is not considered a preferred approach, as most flooring manufacturers may consider these substances "contaminants" that could compromise the integrity of the flooring and the bond to the substrate. Moreover, there is no good way to test their effectiveness.
Another approach is to use an acrylic adhesive when installing the floor. However, while these adhesives may claim to withstand high relative humidity (RH) levels, acrylics can degrade with sustained exposure to high moisture and pH levels.
Contact a Flooring Specialist today
The traditional approach to moisture mitigation is the use of a two-part epoxy to seal the slab surface, providing a dry substrate for the floor. While effective, this method requires multiple coats and a long cure time, potentially delaying the project schedule. In addition, whether installing in a new or existing slab, the surface must be shot-blasted prior to application, potentially releasing hazardous material into the building, requiring costly containment and worker safety measures. As it cures, the epoxy may release volatile organic compounds (VOCs), which are known to be hazardous.
A less invasive strategy is to apply a floor underlayment (rolled moisture barrier) to the concrete slab prior to installing the finished flooring. Barriers have been shown to stand up to RH levels as high as 99.5% and pH of 12 over an extended period of time. They can be applied rapidly, saving time and labor and they do not require potentially hazardous surface preparation processes or caustic chemicals.
Before choosing your moisture mitigation approach, consider some important questions. How high are moisture levels in the slab? Does your contract expose you to potential liability for moisture damage—and, if so, for how many years? Could releasing potentially hazardous materials impact workers or, in the case of renovation projects, building occupants? Is speed of application a priority?
The answers to these questions will help guide you to a moisture mitigation strategy that protects you, the building owner, and the building occupants for many years to come.
Tags
- Airports
- Architects
- Arts & education
- Commercial buildings
- Contractor
- Energy facilities
- Engineer
- Flooring
- Industrial facilities
- Museums
- Repair and Renovation
- Residential buildings
- Retail buildings
- Schools
- Sports stadiums
- Subcontractor
- Underlayment
- VersaShield